Getting the most of Hydraulic Breakers: Expert Tips for Construction and Demolition Projects
Dario Giraudo, Product Manager, Rotair
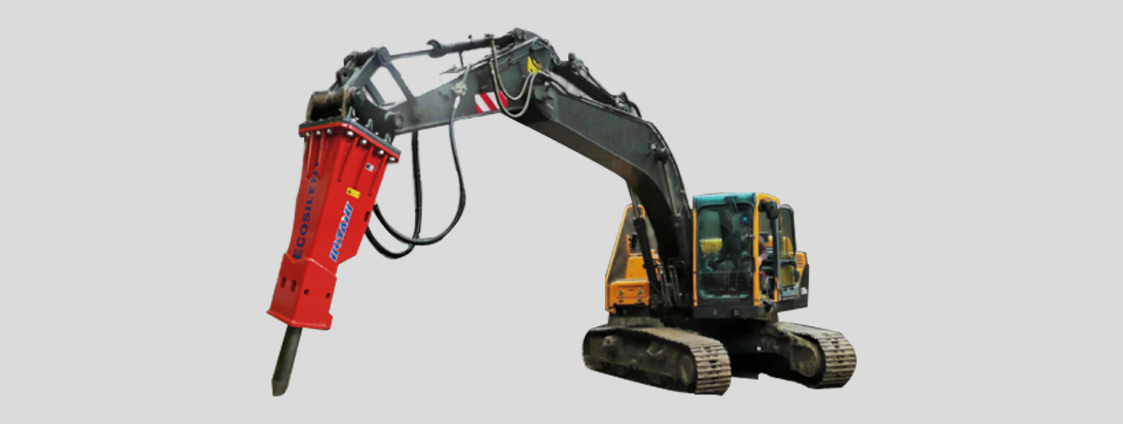
Hydraulic breakers are as common as they are indispensable in construction and demolition, providing unmatched power and precision. With various designs, sizes, features, and functionalities available on the market, selecting the right tool requires a thorough understanding of the technology to ensure efficacy, productivity, and cost-effectiveness of projects.
This article covers the practical aspects of hydraulic breakers, providing guidance through the selection process.
Finding the Right Size
Ensuring peak performance and cost-efficient functionality hinges on selecting the appropriate hydraulic breaker for specific requirements. The applications and materials the breaker will most frequently encounter dictate the choice, which means that the quantity, condition and composition of material requiring fragmentation must be assessed. Smaller breakers excel with medium-density materials such as concrete or asphalt. Naturally, small/medium-sized breakers are suitable for use with compact machinery like mini excavators. Medium/large-sized breakers, on the other hand, are recommended for use with excavators for heavier tasks on tough materials like rock or for use in quarries.
Assessing Power
Evaluating the power and the corresponding size of the hydraulic breaker paired with the excavators involves factors such as the weight and hydraulic characteristics of the carrier excavator and the type of use – whether continuous or service-oriented. The breaker must be matched to the excavator in a manner that is compatible not only with its mass but also with the appropriate oleodynamic characteristics (oil flow, oil pressure) of the excavator
Matching a hydraulic breaker that is too small to an excavator in an unbalanced manner can lead to malfunction and reduce its durability, as well as poor performance during operation. Conversely, pairing a carrier machine, such as a mini excavator, with a breaker that is too large in terms of mass and hydraulic characteristics can cause power supply issues to the breaker and operational functionality problems in the machine's movement, leading to potentially dangerous imbalances of the excavator and safety risks. Additionally, this does not optimize the hydraulic compatibility between the machine and the breaker, resulting in limited power generated by the breaker.
Reliability and longevity
The production criteria used in the manufacturing processes of hydraulic breakers, such as the forming of its components, heat treatment, and the specific grinding phases of the parts, are crucial for its reliability and durability. High-grade, certified steels, meticulously processed in state-of-the-art machining centres with continuous computer monitoring and certified heat treatment stages, ensure product quality.
A point of extreme importance in the mechanical processing of the breaker parts is represented by the grinding phases, conducted through multiple steps and grades, that produce specular and robust surfaces and an excellent finish. Such meticulous attention to detail ensures optimal demolition efficiency and longevity.
Considering Unique Features
High quality hydraulic breakers often come equipped with a high-pressure nitrogen accumulator with a membrane, acting as a hydraulic spring. This function allows for increasing the energy and striking power of the breaker itself on the material to be demolished. Additionally, this membrane-based accumulation system reduces internal vibrations within the breaker, resulting in less operational stress
Streamlining Maintenance
Efficient inspection and replacement processes save valuable time and rely on the easy disassembly of internal components. Quick access to internal components without specialised tools is also advantageous.
The body of the breaker, or striking body, comprises three main components (head, cylinder, and back head/forehead). Inside the head, we find the distributor, which manages the striking and frequency of the breaker on the material to be demolished. The nitrogen accumulator is typically located on the top of the head. The forehead contains wear-resistant bushings that are easily replaceable and are in direct contact with the demolition tool. Construct with quality materials ensures the correct guide to the tool during demolition, and provides specific greasing points to reduce the wear of the bushing, ensuring a long service life.
High-quality breakers feature a modular design with minimal moving parts. This allows for reduced wear, risk of breakage, and consequent costs over the operational life of the breaker
Extending the lifespan
The lifespan of breakers heavily depends on maintenance practices. A well-maintained breaker can last more than 10 years, depending on regular maintenance, adherence to regulations, and the use of manufacturer-specified spare parts. It is crucial to adhere to the manufacturer's recommended maintenance schedule to prevent internal contamination, such as dirty oil or moisture, which can damage internal components
Top brands provide equipment for monitoring the nitrogen charge within the breaker accumulator. Adhering to the charge value specified in the owner’s manual, typically recommended for annual inspection, is essential for optimal efficiency. Correct nitrogen pressure for the accumulator is crucial for optimal performance of the breaker.
By understanding these critical factors, professionals can select and maintain hydraulic breakers that offer optimal performance, longevity, and cost-efficiency in construction and demolition projects.